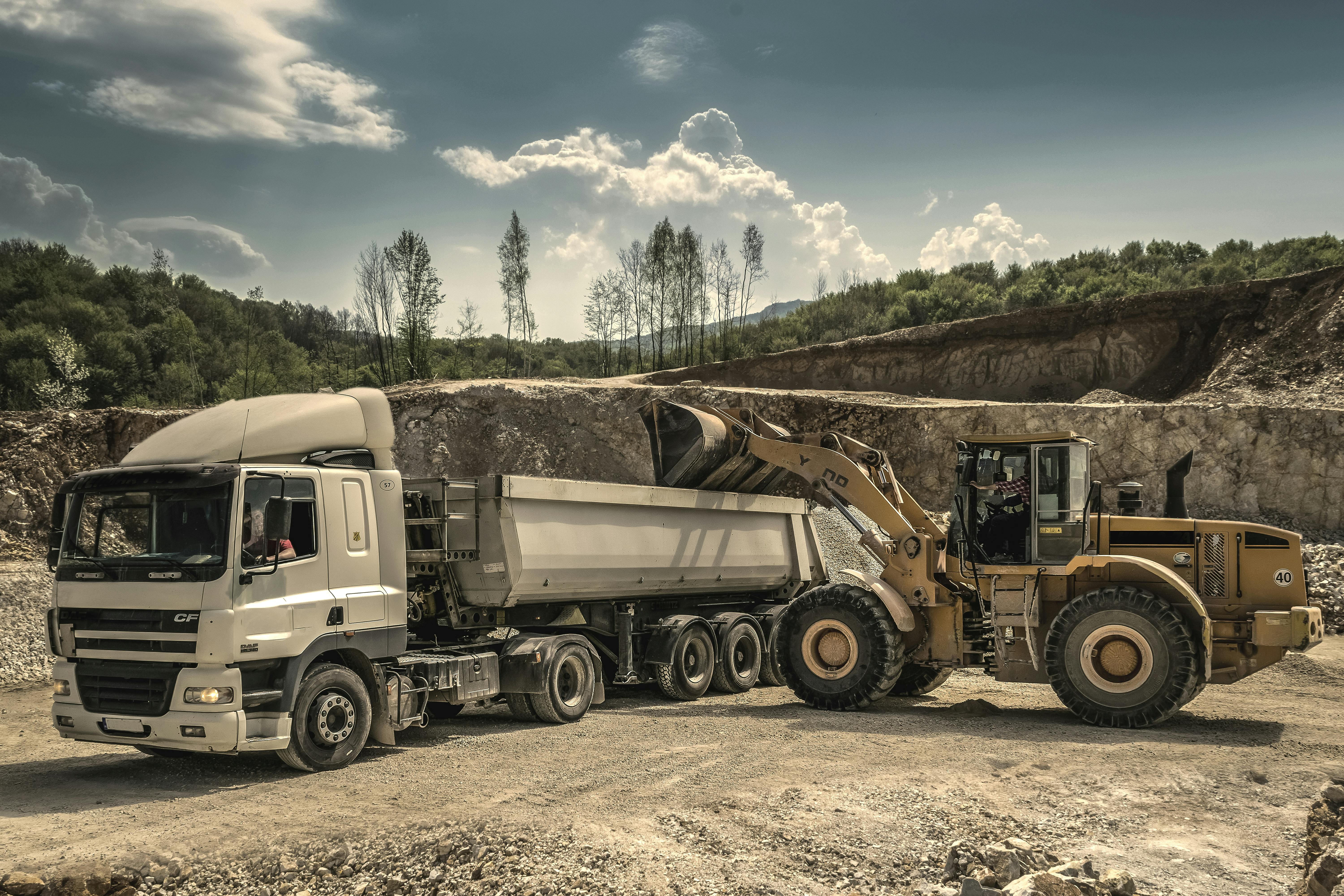
In a sector where every minute counts, managing truck flows and loads remains a major challenge for site managers and logistics managers in aggregate quarries. Between the need to optimize incoming and outgoing flows, to ensure regulatory compliance and to limit operational costs, the challenge is significant.
Problem: time-consuming and poorly optimized flow management
Expensive traffic jams and delays
Traffic jams and site delays cause significant time losses and directly affect productivity. Poor management of truck flows can generate extended waiting times, thus slowing vehicle turnover and increasing operating costs. An immobilized truck is an immediate financial loss for the company.
👉 The estimated delay rate is 15%, which represents an average loss of 45 minutes by truck and per day,
👉 The average hourly cost of agents is estimated at 20-30 €/h, which implies a financial loss of 15 to 22.5€ by immobilized truck,
👉 For a career dealing 100 trucks per day, this represents an annual financial loss of up to €100,000 simply because of the accumulated delays.
Manual traceability that is a source of errors
The traceability of materials is often inaccurate, with manual monitoring that multiplies the risks of errors and disputes. Paper documents, manual entries, and non-centralized exchanges increase the risks of inaccuracy and information loss, undermining the transparency of operations. The Estimated percentage of administrative errors Is of 10 to 12%, representing a cost ranging from €50 to €100 per error, which can quickly lead to significant financial losses for businesses.
Time-consuming regulatory reporting
Complying with legal requirements for monitoring aggregate flows requires rigorous work and careful document management. This administrative burden mobilizes significant resources and exposes sites to risks of non-compliance, with significant financial consequences.
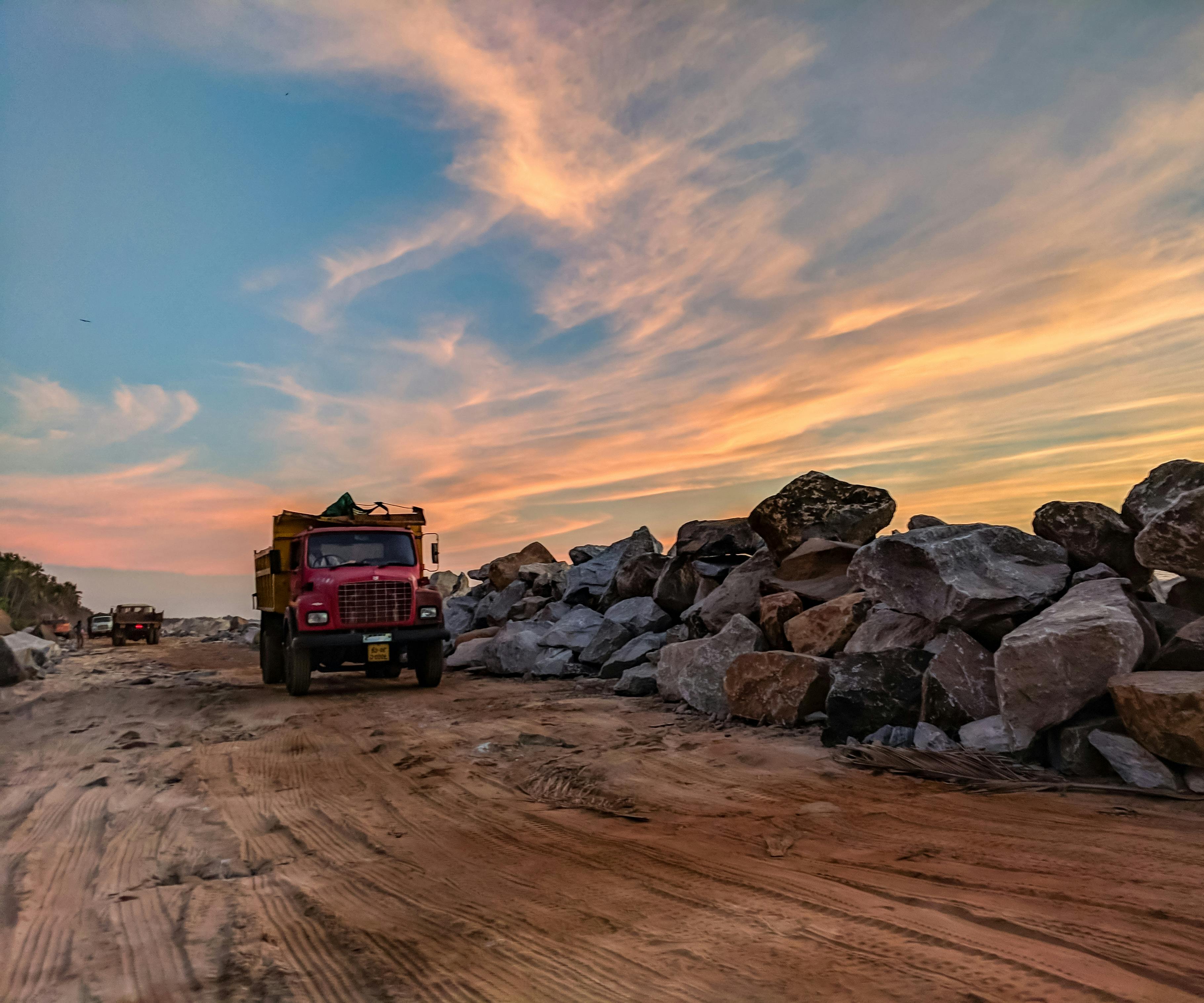
🚀 Dune: an innovative solution to streamline flow management
Automating flows for more efficiency
With the Synaxe Dune terminal, the automation of flows via digital terminals allows a 15% reduction in delays, i.e. an average gain of 45 minutes per truck per day. By streamlining entries and exits, quarries notice additional truck rotation, thus improving the overall productivity of the site.
Digitalization and traceability in real time
Digitizing and centralizing data via Dune reduces input errors by 15%. Each transaction is recorded automatically, ensuring complete traceability of incoming and outgoing flows. This limits losses and allows rigorous monitoring of loads in real time.
Simplified regulatory compliance
Dune simplifies regulatory monitoring and compliance (REP, DAP) by automating reporting, saving logistics managers 5 hours per week. The solution also reduces the risk of fines related to non-compliance, up to €20,000 per year.
📊 The benefits in key figures
Reduced costs and errors
- ✅ 15% reduction in delays, saving 45 minutes per truck per day
- ✅ An additional rotation per truck thanks to the optimization of flows
- ✅ 15% fewer input errors thanks to digitization
Saves administrative time
- ✅ 5 hours saved per week for follow-up and compliance
- ✅ Reduction of time-consuming administrative tasks
Financial optimization and compliance
- ✅ Average annual savings of €5,000 on the costs of correcting errors and disputes
- ✅ Reduction in potential fines: up to €20,000 per year
Dune: a strategic asset for careers
Investing in the Dune terminal means choosing a more fluid, more precise and more economical management of career flows. With measurable gains and better control of operations, this solution is a strategic asset for careers that want to improve their performance while ensuring compliance. Digitalization is thus becoming an essential lever to meet the productivity and profitability challenges of the sector.