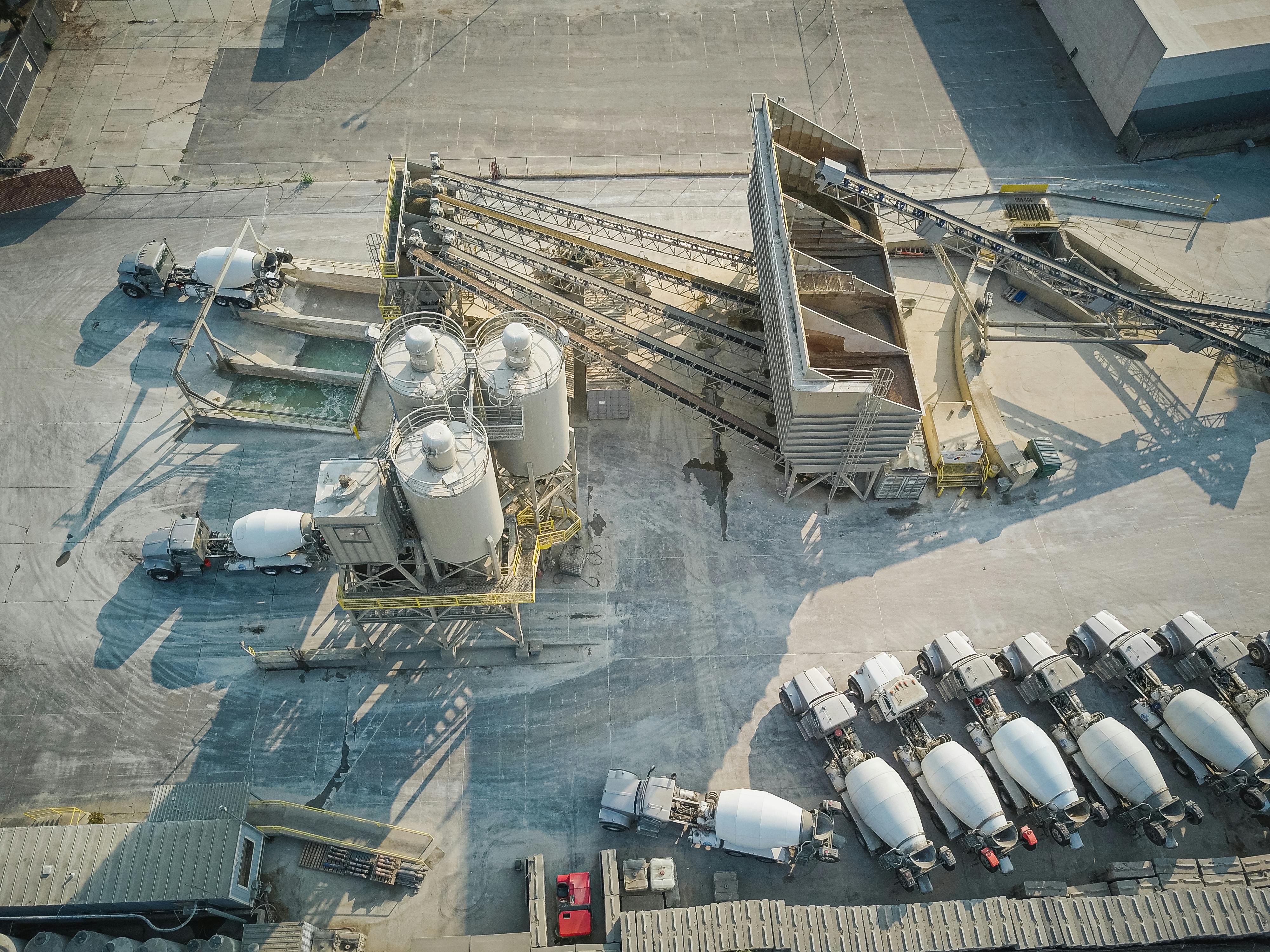
In the construction sector, ensure a production of quality concrete is a priority for concrete batching plants. Optimized management of raw material supplies — aggregates, cement, cement, water and additives — is essential to ensure homogeneous mixtures, meet deadlines and minimize costs. This article explores best practices for improving concrete quality by optimizing supplies, a crucial issue for concrete plant managers.
1. Why optimizing supplies is essential for concrete quality
A concrete plant depends on the constant supply and quality of its raw materials to produce concrete that meets technical specifications. Fluctuations in the quality or quantity of materials can compromise the homogeneity of mixtures and cause productivity losses.
2. Common challenges in managing supplies for concrete batching plants
Managing supplies in a concrete batching plant involves several challenges:
1- Variability of delivery times
Delivery times for raw materials (such as cement, aggregates, or additives) may vary depending on several factors such as weather conditions, logistical disruptions, or carrier delays.
These variations complicate production planning, especially when concrete demand is high or subject to sudden spikes.
2- Management of raw material stocks
Concrete batching plants must maintain a delicate balance between sufficient stocks to ensure production and optimal storage levels to avoid unnecessary costs or deterioration.
Poor management can lead to stockouts or excessive capital immobilization.
3- Fluctuating material quality
The quality of raw materials may vary between suppliers, quarries, or even transport and storage conditions.
These variations directly affect the performance of concrete (strength, durability, workability), which can lead to claims or additional costs to adjust formulations.
4- Communication between suppliers and production teams.
Inefficient or delayed communication between suppliers and internal teams can cause errors in deliveries, misunderstandings about required quantities, or incompatibilities in schedules.
This can disrupt production schedules and cause financial losses.
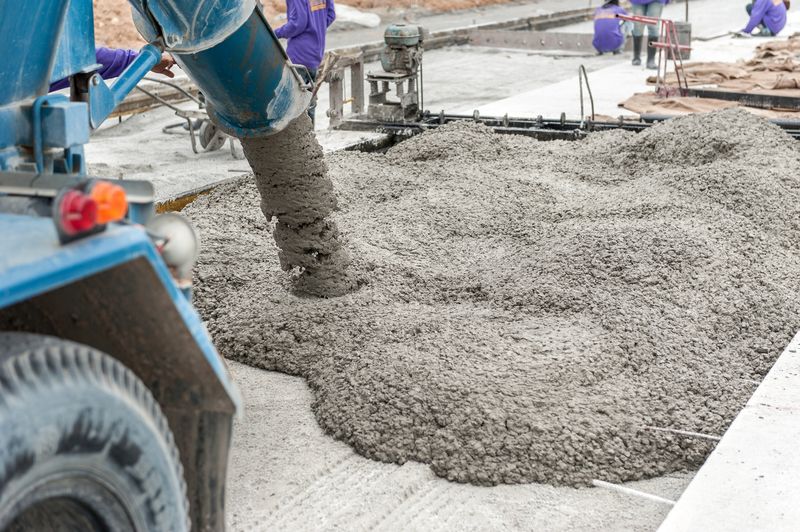
Concrete delivery note: 3 reasons to use it
3. Improving quality and customer service through digitalization
The optimization of supplies and deliveries goes far beyond the framework of a simple logistics process. For concrete batching plants, these aspects represent major levers for guaranteeing quality, productivity, and profitability. Digital platforms like Dune make it possible to better anticipate needs, ensure rigorous monitoring of materials, and maintain consistency in the quality of concrete. This control is all the more crucial when we know that variations of only 2% in the dosage of aggregates can significantly affect the strength of concrete, while a 5% variation in the water content can reduce its durability by more than 20%.
Take the example of a concrete plant producing an average of 300 cubic meters of concrete per day. By adopting an integrated supply and delivery management solution, it can reduce costs by 10% by avoiding overstocking, delays, and losses due to non-compliant materials or processes. This represents an annual saving of several tens of thousands of euros, while ensuring total compliance with quality standards.
In the field of deliveries, tools like SX Delivery by Synaxe play an essential role. This application makes it possible to manage deliveries from concrete plants in real time with key functionalities such as monitoring waiting times on site, adjusting water volumes directly on site, and optimizing pump management. These digital tools also provide greater transparency, offering real-time reports to track each stage of the delivery process.
In addition, the management of raw material supplies can be automated and optimized 24 hours a day by setting up entry terminals on sites, particularly useful for those located in urban areas. These terminals make it possible to streamline incoming flows, improve the traceability of materials, and guarantee the constant availability of resources, while reducing the nuisances associated with unplanned deliveries.
With such a combination of digital tools, power plants can reduce errors and delays related to deliveries and supplies by 15%. They thus ensure better management of resources, increased respect for production deadlines, and optimized profitability. By effectively connecting production operations, supplies and construction site needs, the Dune Suite and its modules such as SX Delivery transform processes into strategic levers for performance and customer satisfaction.
Contact us to discuss your project | Synaxe